New Compact Design
ATS’s new tapping units are designed to be the most reliable and compact unit available today. Our 20 year experience in the tapping business enabled ATS’s engineers to combine a totally new drive train with our proven twist lock lead screw assembly. The following features show ATS’s commitment to improve our customers efficiency and productivity:
High Speed: ATS’s new high speed tapping units have been tested up to 250 strokes per minute. Most in-die tapped parts rarely exceed 150 strokes per minute, but when higher production rates are feasible, our new tapping units will maximize your production.
Reliable: ATS’s new high tork drivers use larger hardened gears and shafts plus roller and ball bearings throughout the gear train. These design improvements not only increases the capacities of all our models but assure a long trouble free life.
Twist Lock Design: ATS’s twist lock lead screw assembly has many unique features incorporated into a very compact unit. With our lead screw assembly, tap changes are made outside the die, this is not only safer but faster and easier for the operator. Misfeed protection is also incorporated within the assembly. If misfeed occurs, a spring loaded safety will prevent tap breakage and any additional stress to the gear train. Our lead screw assembly uses standard cutting or roll form taps. This allows our customers to select the best the most competitive taps for their tapping operations.
Durable: All housings are constructed from solid steel using the latest CNC technology. Solid steel construction allows ATS’s units to be the strongest and most compact available.
Rapid Advance & Bottom Up Models
Dies with higher material lift require a different approach to IN-DIE TAPPING. ATS gives it’s customers an option to tapping from the bottom up or top down using an air activated rapid advance lead screw assembly.
Rapid Advance: The air activated rapid advance tapping unit basically functions the same as a standard tapping unit by replacing the standard twist lock lead screw assembly with a rapid advance lead screw assembly. The rapid advance tapping unit still maintains the same lead screw accuracy to advance the tap, thus producing the same quality threads as our standard tapping unit. Rapid advance technology decreases rpm while increasing tap life and makes higher lift tapping dies feasible.
Bottom Up Tapping: Tapping from the bottom up is another approach to higher material lift tapping dies. Parts with small diameter tap holes and lower material lift may run faster when tapping from the bottom up. ATS’s bottom up tapping units use the same twist lock lead screw assembly as our top down tapping units. Additionally, a new optional “Quick Change” system, allows our customers to change taps from the top of the unit, while maintaining all the safty features of our standard lead screw assemblies. Whether tapping from the bottom up or top down ATS’s engineers will work closely with your designers to recommend the best tapping unit for your application.
Features
- Press speed up to 250 strokes per minute
- Compact design requires less die space
- Simple Installation
- New high tork driver extends service life
- Removable twist lock lead screw assembly
- Change tap in seconds outside the die
- Use standard cut or roll form taps
- Lead screw tapping assures quality threads
- Through the tool coolant
- Misfeed protection prevents tap breakage
- Change tap size and pitch in only minutes
- Solid steel construction
- Change from die to die in minutes
- Capacity 2-56 to 1 ¼”-12
- Made in the USA
Special and Multiple Spindle In-Die Tapping Units
Multiple spindle tapping units have distinct advantages over individual in-die tapping units. Parts with multiple tapped holes can often be tapped in a single station which saves die space and tooling costs. With ATS’s twist lock lead screw assembly any combination of pitch and tap diameters can be combined in a single multiple unit. ATS’s new TH-55 high tork driver can tap as many as eight 5/16″-18″ holes in a single tapped part. We specialize in custom in-die tapping units built to customers specifications. Whether a tapped part has three #4-40 or five 3/8″ – 16″ tapped holes, ATS will build a top down, bottom up, or rapid advance multiple spindle in-die tapping unit to fit our customers requirements while keeping costs to a minimum.
Working Specifications
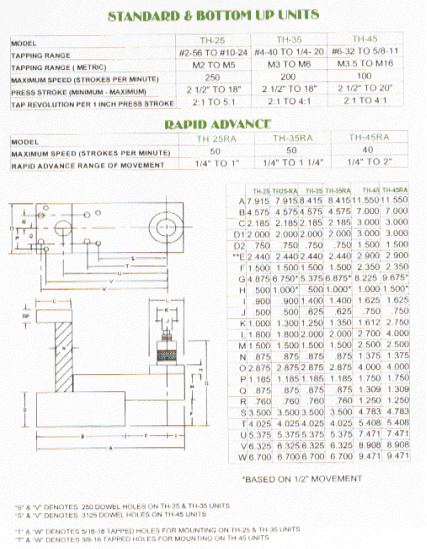
In-Die Tapping Design Considerations
The major differences between a tapping die and a non-tapping die are longer stripper travels and allowing enough space or progressions for the tapping unit. Most existing non-tapping dies can be split and remounted into a larger die set to accommodate the space required for the tapping head. The following are some of the considerations and possible modifications needed when designing a tapping die.
Material Lift: When tapping from the top down material lift should be kept to a minimum. The less the material lifts, the less the tap will have to travel. Less tap travel translates into lower RPM and higher production rates. When the part requires a higher material lift, tapping from the bottom up or top down with the use of a rapid advance lead screw assembly may be required to maintain higher production rates. Your factory representative will be glad to discuss the best method for your tapping application.
Stripper Travel: Most tapping dies will require longer stripper travel then non-tapping dies. In most cases, the stripper will have to hold the material the entire time the tapping process is taking place. Such variables as material thickness (plus extrusions) or any forms that may affect the length of tapping time will determine the actual stripper travel. Spring strippers are the most common method used in tapping dies, though in many cases a bridge stripper may be used in relatively flat running parts. If a bridge stripper is used it is still advisable to have spring pushpins located on either side of the tapping unit to hold the material down during the tapping operation. In some cases, air activated hold-downs located on either side of the tapping unit have also been a successful method of holding the material during the tapping process. Whichever method is used it is important to properly calculate the length of stroke that is necessary to hold the part during the tapping operation. Your factory representative will be able to help you calculate the length of stroke that is needed to determine your stripper travels.
Piloting: When designing tapping dies proper piloting is always recommended. Proper hole location will aid in providing longer tap life and higher production rates. Due to the longer stripper travel tapping dies usually require longer pilots. It is always best to have the pilots enter the material prior to the tap entering the material. However, in some cases it is not practical to use such long pilots, especially when they are a smaller diameter. In some cases, it may be necessary to place the pilots in a guided stripper or in the lower die section. It should be noted the ATS tapping unit provides enough clearance in the lead screw assembly to allow for slight progression adjustments.
Clearances for Tapping Unit: The standard ATS tapping unit requires two clearance holes in the die set, one in the upper die shoe and one in the lower die shoe. The upper die shoe requires a clearance hole for the complete lead screw assembly, including the lead screw assembly holder (ref. ³L² dimension in the working specifications of the ATS literature). The other necessary clearance hole in the lower die shoe will be for the camshaft (ref. ³N² dimension in the working specifications of the ATS literature). By providing these two clearance holes the shut height between the two die shoes will be lowered to accommodate the basic tapping unit lower and tap drive housing. If less shut height is required then additional clearance for the housings themselves can be provided. Please note, if upper die shoe thickness is not thick enough to provide vertical clearance for the lead screw assembly (ref. ³G² dimension) plus clearance for the lead screw, additional upper Parallels may be needed. Clearances for the lead screw assembly and the camshaft in a bottom up tapping unit are needed in the lower die shoe only. It is helpful to provide hand clearance to allow for removal of the lead screw assembly. If it is not practical for lead screw assembly removal, some bottom up tapping units have a quick change tap option which will make lead screw assembly removal unnecessary for tap changes. Also note vertical clearance will be needed under the tapping unit equal to the press stroke for the camshaft in the lower die shoe, this is standard in all models. All referenced dimensions will require additional clearance than actual dimensions.
Camshaft Engagement: It is always important to maintain proper camshaft engagement. In order to ensure proper engagement, the upper camshaft mounting block should be within one half inch of the lower drive housing in the closed position. In some cases it may be necessary to pack the upper camshaft mounting block to maintain this minimum distance. Please note provided there is clearance for the camshaft under the tapping unit, a higher stroke tapping unit can always run in a lower stroke punch press. If it is necessary to run a lower stroke tapping unit in a higher stroke punch press, it will be necessary to purchase a camshaft designed equal to the stroke of the press.
Strip Clearance: Strip clearance between the tapping unit and the lower die section will vary depending on the material thickness and lift. Another consideration when determining strip clearance is to allow for the addition of a wear plate mounted to the outer tap drive housing, and necessary coolant tubes for the tap. Often the coolant tubes can be incorporated into the wear plate. In many applications a wear plate is not necessary and coolant tubes can be mounted under the tapping unit. If for any reason the ³F² dimension (from the working specifications of ATS literature) does not provide enough clearance it will then be necessary to place a packing plate under the unit. If the hole to be tapped is further from the edge of the strip then the ³E² dimension (from the working specifications of ATS literature) provides, then a special long ³E² dimension tapping unit can be provided.
Press Stroke: Tapping dies will usually require a minimum of three inches of press stroke though on relatively flat running dies two and a half inch press stroke have been sufficient. Higher press stroke may be necessary on dies with higher material lift or a very fine pitched tapped hole. ATS tapping units are available with different gear ratios, which will compensate for very high tap movement on long stroke presses.
Gear Ratio: ATS tapping units have three standard available gear ratios, 2 to 1, 3 to 1, and 4 to1 on theTH-35, TH-45 and TH-55 models. The TH-25 model has one additional gear ratio available of 5 to 1. Simply stated gear ratio refers to the number of revolutions that the tap will make per one inch of press stroke. Example being a TH-25 tapping unit with 5 to 1 gear ratio in a four inch stroke press will make twenty revolutions clockwise and twenty revolutions counter clockwise per press cycle. As a general rule, lower stroke presses will use higher ratio tapping units. Once the number of required revolutions for a particular tapping die is determined press stroke and gear ratio can be calculated. Special gear ratios are available upon request. Your factory representative will be able to help determine which gear ratio is best suited for your application.
Tapped Hole Diameter: Proper tapped hole diameter is crucial for maintaining high productions rates and long tap life. In many cases, one or two thousandth difference in hole diameter will make a major difference in the over all performance of a tapping die. This is particularly true when formed taps are used, which account for ninety-five percent of all in die tapping dies. Example: 10-32 form tap with a 65% thread uses a .176 diameter hole. A one thousandth decrease in diameter or .175 hole increases the percentage to 75%. This demonstrates how only a few thousandths difference in tapped hole diameter can make a major difference in the percentage of thread. As a general rule, a tapping die will run best when the lowest expectable thread percentage is used. It should also be noted that a roll form thread would consistently out torque a cut thread of the same percentage, which can result in using a lower percentage thread and still maintaining the torque requirements of the tapped hole. It is also important to remember when determining proper hole size that a cutting tap uses a much smaller hole then a form tap. The ³H² classification of the tap should also be taken into consideration when determining hole size. Higher ³H² classifications will require a larger diameter tapped hole.